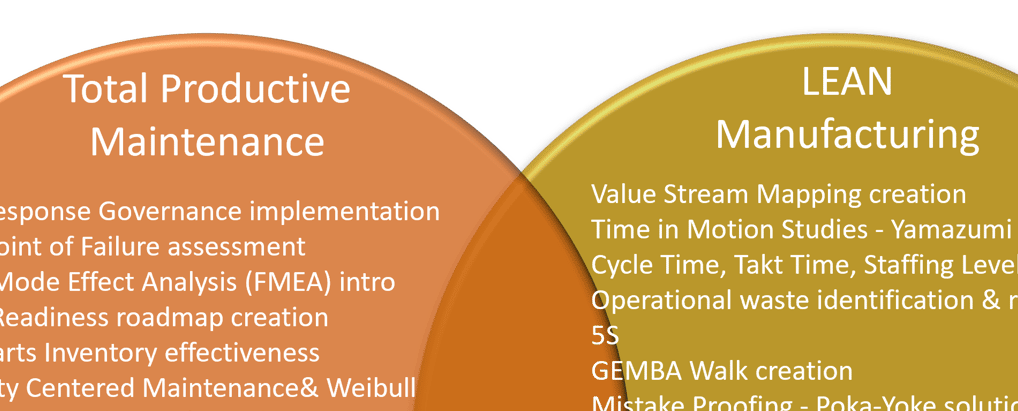
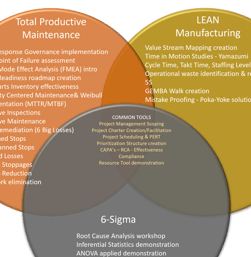
Have you ever heard ...?
Get out of the Crisis! “Remove barriers that rob people of pride of workmanship…”
"We have all the spare parts needed in inventory. We have never purchased parts from e-bay.”
“ Our site's plant projects are prioritized effectively. We have all the resources needed.”
“Our CAPA Effectiveness Verifications pass with flying colors every time”.
“All of our CAPA's are closed effectively and on-time. Nobody asks for extensions."
"Auditors and Inspectors rarely find non-conformities in my operation”.
“Night shift personnel have everything they need to fix production issues.”
“Our equipment and tooling rarely fail. Maintenance complete their PM's effectively.”
“After every service event, our equipment runs like a charm.”
“We complete every project on time and within budget.”
“We have plenty of technical experts in all shifts and they are happy working here."
Industry Observations
Root Cause Analysis-tools and practices to identify underlying causes of non-conformities and CAPA’s could enable the formulation of effective corrections, corrective actions, and preventive measures.
Plant program/project priorities are normally defined at the Leadership Team level. Resource loading is rarely visible at this level and when 'doers' are overloaded, priorities are diluted, and projects lose their ranking leading to complacency and missed commitments.
Improper service frequency including over-servicing may be in-place. Many PM activities are adopted from equipment manufacturers during installation qualification and those may not be based on your specific application or your appropriate duty cycle.
When failure recovery governance is not defined. First responders may find themselves alone, without support and frustrated. Establishing an internal Rapid Response program with rules around severity, escalation and communication have proven to reduce recovery time, reduce blame, increase accountability, and transform collective learning.
Spare Parts inventory may not align with your areas of risk. Equipment supplier often recommend spares based on mechanical wear. We continue to find that the entire electrical and controls overarching system is often excluded when assessing the spare parts inventory requirements. A Systems Risk-based spares inventory approach may decrease your inventory size and reduce your time to recover from hard breakdown failures. This approach may also reduce your parts inventory cost over time.
If you have, this site may not be for you.
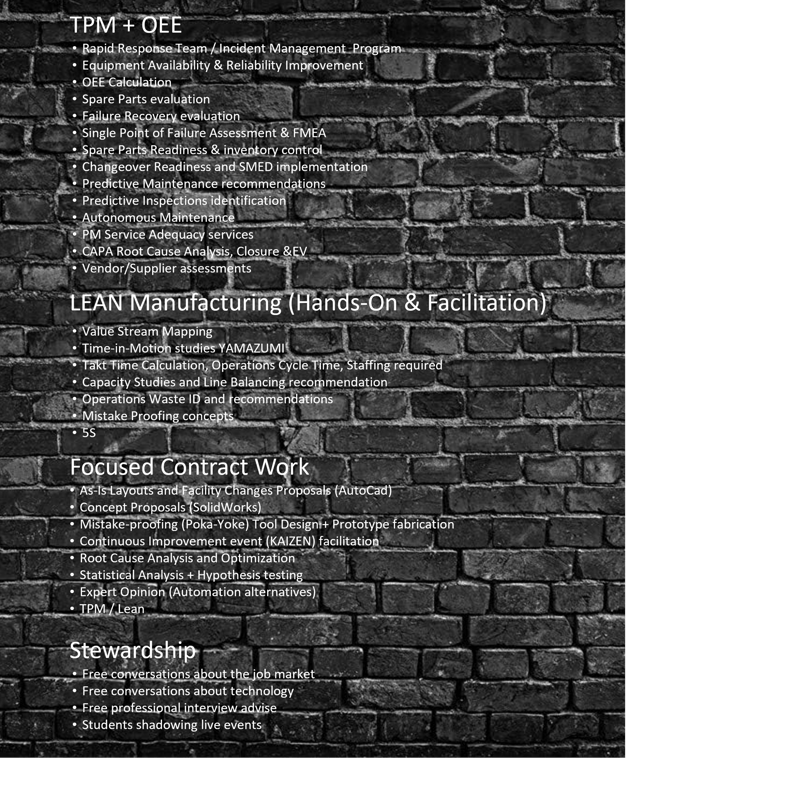
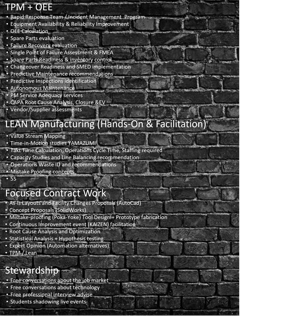
At Integral OEE we help Organizations re-establish their competitive spirit by removing hidden operational obstacles using Operational Excellence tools
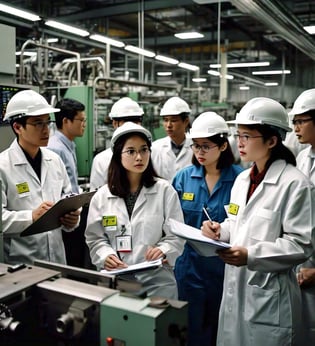
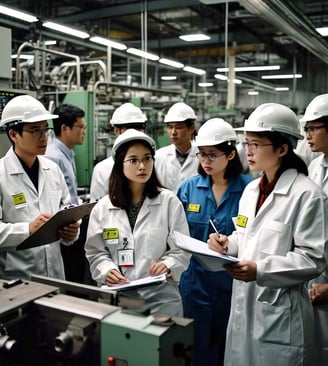
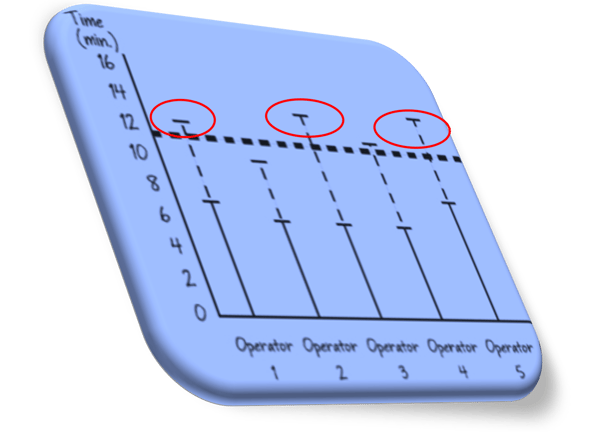
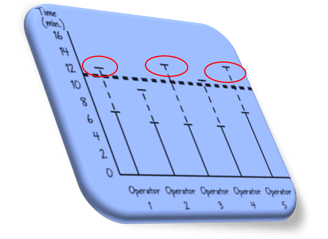
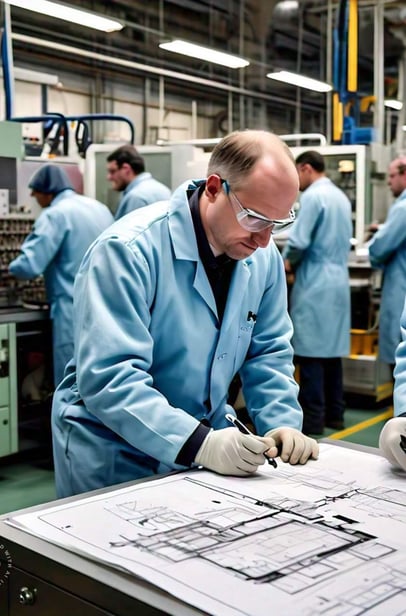
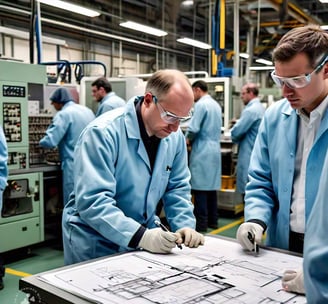
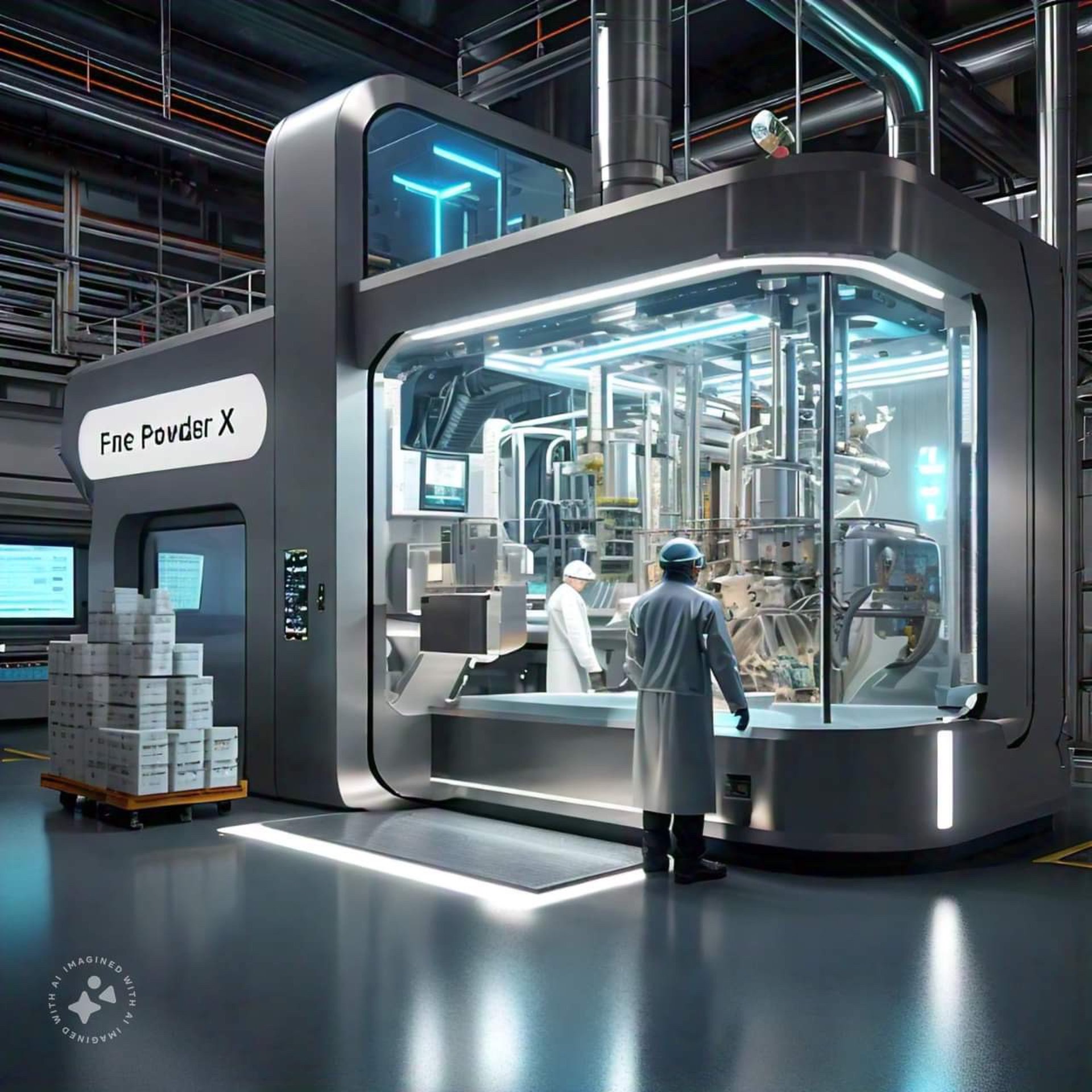
We help your leaders return to the workplace ready to re-engage and to compete using Operational Excellence tools
Impact
Support
Results
We have a PRAGMATIC approach! The Operational Excellence tools that we will equip you with will create immediate value and will transform your organization. We apply the tool that best matches your need.
Practical applications of Operational Excellence tools including Six Sigma, Lean Manufacturing, Total Productive Maintenance and Project Management will give your organization a competitive edge
We are results-driven. Our Consultants will go out of their way to ensure that you get true value since day ONE. With dozens of Kaizen events on their belts and 30 years of experience your team is bound to adopt and propagate best practices in the rest of your organization.